Uncovering the Intricate Art of A Weaver’s Beam: A Journey into Timeless Craftsmanship
Have you ever heard the saying, “stronger than a weaver’s beam”? This phrase has long been used to describe something or someone that is sturdy and resilient. But what exactly is a weaver’s beam? In the world of weaving, it holds a significant role as the framework for textile creation. A weaver’s beam may seem like an insignificant tool, but its importance in the weaving process cannot be overlooked. In this article, we will delve into the history, function, and significance of this unassuming yet essential piece of equipment known as the “weaver’s beam.”
The History of Weaver’s Beams
Weaver’s beams have been an essential tool in the textile industry for centuries. The earliest recorded use of a weaver’s beam dates back to ancient Egypt, around 3500 BC. These early beams were made of wood and were primitive compared to modern weaver’s beams.
As the textile industry evolved and became more advanced, so did the weaver’s beam. In the 19th century, looms became industrialized, and larger quantities of fabric were produced at a faster rate. This led to the development of more durable and efficient weaver’s beams.
During this time, many innovations were made to improve the design and function of the weaver’s beam. These advancements included using metal instead of wood for added strength and introducing sectional beams that allowed for different colors and designs to be woven simultaneously.
In the 20th century, with the rise of technology, electronic devices such as sensors and tension controls were incorporated into weaver’s beams to enhance their performance. Today, computer-controlled looms are widely used in the textile industry, which has further revolutionized how weaver’s beams are used.
The Anatomy of a Weaver’s Beam
A weaver’s beam consists of several components that work together to hold yarn in place during weaving. These components include the warp beam, cloth roll, and various mechanisms for tension control and yarn guiding.
The warp beam is a large cylinder that holds the lengthwise threads (warps) under tension before they are fed through the loom system. It is typically made of metal or wood with flanges on each end to keep the warp threads in place.
The cloth roll is another crucial part of a weaver’s beam. It is responsible for winding up the woven fabric as it comes off the loom. This roll moves in opposition to the warp beam during weaving, creating tension in the fabric.
Weaver’s beams also have mechanisms for controlling tension and guiding the yarn. These include tension bars, which add or reduce pressure on the warp beam, and disc brakes, which help to maintain tension on the warp threads.
The Importance of Weaver’s Beams in Textile Production
Weaver’s beams play a critical role in textile production as they hold the warp threads under tension, making it easier to weave efficiently and produce high-quality fabrics. Without an adequately functioning weaver’s beam, it would be impossible to create complex patterns or multi-colored designs.
Furthermore, weaver’s beams also contribute to the speed and precision of textile production. A well-designed beam with proper tension controls allows for a faster weaving process with fewer errors. This ultimately translates into increased productivity and reduced production costs.
Modern weaver’s beams are also designed with ergonomics in mind, allowing operators to work comfortably and efficiently for extended periods. This is especially important as textiles are still largely produced by human labor.
The Different Types of Weaver’s Beams
There are various types of weaver’s beams available for different purposes and applications. The most common types include industrial sectional beams, flexible rapier beams, positive drive rapier beams, air jet weaving systems, and projectile beaming systems.
Industrial sectional beams have adjustable widths to accommodate various fabric widths. They are often used in high-speed looms that produce large quantities of fabric at a rapid pace.
Flexible rapier beams use a rapier pick-up system that helps project the weft thread across the warp threads during weaving. Positive drive rapier beams have positive drive mechanisms that maintain constant pick-up speeds regardless of loom speed.
Air jet weaving systems are highly automated and use compressed air to propel the thread across the warp threads during weaving. Projectile beaming systems use small metal projectiles to insert yarn into a shed at high speeds.
Each type of weaver’s beam has its advantages and is suitable for different types of fabrics and production needs.
The Future of Weaver’s Beams
The textile industry is continuously evolving, and so are weaver’s beams. Today, researchers are exploring new ways to improve the design and function of weaver’s beams to make them more efficient and sustainable.
Some advancements that have been made in recent years include using carbon fiber instead of metal or wood for added strength and reduced weight. There is also ongoing research on developing electronics and software that can further automate the weaving process, leading to increased production efficiency.
In terms of sustainability, there is a growing focus on using renewable materials for weaver’s beams, such as bamboo or recycled plastic. This will not only reduce the environmental impact but also contribute to cost savings in the long run.
Ultimately, the future of weaver’s beams looks promising as technology continues to advance, leading to even more innovative designs and capabilities. These developments will undoubtedly have a positive impact on the textile industry as a whole.
What is A Weaver’s Beam?
A weaver’s beam is a key component of a weaving loom, which is a machine used to create woven fabric. It is a long, sturdy wooden or metal bar that runs horizontally across the width of the loom. The warp threads of the fabric are wound onto the beam and then fed through other components of the loom, such as the heddles and reed, to create the fabric. The weaver’s beam acts as a support for the warp threads as well as a mechanism for tensioning them properly during the weaving process.
History of Weaver’s Beams
The use of weaver’s beams can be traced back to ancient civilizations such as Egypt, Greece, and China. In these early forms of weaving, a simple horizontal bar was used to hold the warp threads in place. As technology advanced and more complex looms were developed, weaver’s beams became more sophisticated and were integrated into the overall design of the loom.
In medieval Europe, weaver’s beams were often made from solid hardwoods such as oak or elm. They were large and heavy, with holes drilled along their length to hold pegs that would secure the warp threads in place. These beams were integral to the operation of handlooms and played an important role in keeping consistent tension on the warp threads.
With the advent of industrialization in the 18th century, weaving became mechanized and factory-woven cloth became more widespread. This led to changes in how weaver’s beams were designed and used. Instead of having one long beam across the entire width of a loom, multiple smaller beams were used to increase efficiency in production.
The Anatomy of A Weaver’s Beam
A weaver’s beam typically consists of two main parts: the barrel and the ends or cheeks. The barrel, often made of hardwood, is the cylindrical portion of the beam that holds the warp threads. The ends or cheeks, also known as lugs or lobes, are the two protruding pieces at either end of the barrel. They are usually made of metal or hardwood and have holes drilled into them for attaching to the loom.
The ends play an important role in keeping the warp threads in place and under tension. They are attached to either side of the loom, with one end fixed while the other can be moved closer or further away to adjust tension on the warp threads.
Types of Weaver’s Beams
There are several types of weaver’s beams used in different types of weaving machines. One common type is a sectional beam, which consists of multiple smaller beams that can be easily removed and replaced. This allows for quicker and more efficient warping (the process of setting up a loom) as well as easier maintenance.
Another type is a plain beam, which is a solid piece with no sections. These are commonly used on handlooms and smaller industrial looms.
For more advanced industrial looms, there are specialized beams such as double-warped beams, which allow for weaving double-width fabric without having to stop and switch out beams. There are also differential beams used for special weaving techniques that require varying amounts of tension on different areas of fabric.
The Importance of A Weaver’s Beam
A weaver’s beam may seem like a small component compared to other parts of a weaving machine, but it plays a crucial role in creating high-quality woven fabric. The even tension provided by the beam ensures that each warp thread is held in place throughout the entire weaving process. This results in a consistent weave and prevents any warping or buckling in the final fabric.
Additionally, weaver’s beams allow for adjustments to be made during weaving if necessary. If a warp thread breaks or needs to be replaced, the tension on the specific section of the beam can be adjusted without affecting the rest of the fabric.
Modern Developments and Innovations
With advancements in technology, new materials and techniques are being used to create weaver’s beams. Hardwood remains a popular choice due to its strength and durability, but metal beams are also becoming more common, especially for use in industrial looms.
Innovative designs have also been developed to improve the functionality of weaver’s beams. Some beams have adjustable tension systems built into them, allowing for more precise control during weaving. Others have multiple interchangeable sections for different types of fabrics.
In conclusion, a weaver’s beam is an essential component of any weaving machine. Its function may seem simple, but without it, it would be impossible to produce high-quality woven fabric efficiently. From its humble origins in ancient civilizations to its evolution into modern day technologies, the weaver’s beam remains a vital part of the weaving process. As technology continues to progress, we can expect even more innovations and developments in this crucial element of weaving.
Q: What is a Weaver’s Beam?
A: A Weaver’s Beam is a wood or metal rod that forms the foundation of a textile weaving loom, onto which the warp threads are wound.
Q: How does a Weaver’s Beam work?
A: The Weaver’s Beam holds the warp threads taut and consistently separated, allowing for smooth and even weaving of the weft threads.
Q: What are the different types of Weaver’s Beams?
A: The two main types of Weaver’s Beams are plain and sectional. Plain beams consist of a single, solid beam, while sectional beams have individual sections that can be adjusted individually for tension.
Q: What materials are used to make a Weaver’s Beam?
A: Traditional Weaver’s Beams were made from wood, such as maple, cherry, or hickory. Modern beams may also be made from metals such as aluminum or steel.
Q: How do I maintain my Weaver’s Beam?
A: To maintain your Weaver’s Beam, make sure you clean it regularly and remove any buildup of dust or debris. You should also periodically check for any signs of damage or wear and tear, and replace if necessary.
Q: Can I make my own Weaver’s Beam?
A: Yes, if you have woodworking skills and access to appropriate tools, you can make your own simple Weaver’s Beam. However, for more complex features such as sectional beams, it is recommended to purchase one from a reputable supplier.
In conclusion, the weaver’s beam has played a significant role in the textile industry for centuries. From its humble beginnings as a simple wooden device to its sophisticated modern-day counterparts, the weaver’s beam continues to be an essential tool in producing high-quality fabrics. Through this discussion, we have seen that the evolution of the weaver’s beam has been driven by the need for efficient and precise weaving techniques.
The first part of our discussion focused on the history of the weaver’s beam and its early use in manual handloom weaving. We learned that it was initially made from natural materials such as wood and clay and was used primarily in household production. Over time, advances in technology led to the development of more advanced power looms, which also resulted in improvements in the design and functionality of the weaver’s beam.
Next, we explored the different types of weaver’s beams and their respective features. The sectional beam, with its ability to divide fabric into sections for easier handling, has greatly increased efficiency in textile production. The flanged beam, with its grooved edges, allows for better tension control during weaving, resulting in higher quality fabrics. And lastly, air jet looms utilize a pneumatic system to propel a shuttle carrying yarn across the loom at
Author Profile
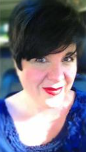
-
My name is Jill but everyone calls me Jilly. I design original cross stitch patterns inspired by vintage French and flowers. Roses are my muse.
I hope you have a cozy time stitching my patterns. Put the kettle on, relax and create a heartwarming piece of hand-embroidered art. Personalize your home and turn up the soulful charm with soulful stitchery.
My goal is to provide you with pretty patterns that promote peaceful stitching. My wish is for you to discover the gentle beauty of hand-embroidery.My patterns have been featured around the web and in Homespun Magazine and Boston Magazine. I find my bliss in cross stitch.
From 2024, I have embarked on a new venture—writing an informative blog on the “Embroidery and Cross-Stitch” niche. This blog is an extension of my passion, where I share detailed posts and respond to queries related to embroidery and cross-stitching.
The blog covers a wide range of topics from beginner tips, pattern creation, historical insights, and the therapeutic benefits of stitching. My goal is to build a community where enthusiasts can learn, share, and grow in their embroidery skills, ensuring everyone can find their own bliss in cross-stitch just as I did.
Thank you to all my customers and readers who have supported Sew French. Your kind emails, photos of completed patterns, and continual encouragement fuel my dedication to this beautiful craft. Join me in stitching a world of beauty and peace, one pattern at a time.
Latest entries
- May 24, 2024Machine Using Tips And MaintenanceUnleashing the Mystery: Demystifying the Purpose of Feed Dogs on a Sewing Machine
- May 24, 2024SewingUnlocking the Magic: Exploring the World of Computerized Sewing Machines
- May 24, 2024SewingUnleashing Creativity: Mastering the Art of Sewing with Fat Quarters
- May 24, 2024SewingTo Wash or Not to Wash: The Great Debate on Pre-Washing Fabric Before Sewing