Master the Art of Crafting Welding Caps: A Step-by-Step Guide on How to Sew!
Sewing welding caps may seem like a daunting task, but with the right techniques and tools, you can create a stylish and functional cap that will last through all your welding projects. Whether you’re a beginner or a seasoned pro, learning how to sew welding caps is a valuable skill to have. Not only does it allow you to personalize and customize your own gear, but it also ensures a comfortable and secure fit for optimal protection. In this article, we’ll take an in-depth look at the steps and tips for creating the perfect welding cap – from selecting the right materials to mastering the most important stitches. Get ready to elevate your welding game with these essential sewing skills!
Understanding Welding Caps
Welding caps are essential protective gear that is worn by welders and other industrial workers. These caps protect the head, neck, and hair from heat, sparks, and other dangers associated with welding. They are designed to fit snugly on the head, covering the ears and forehead while leaving the back of the head open. Welding caps come in a variety of styles, materials, and sizes to cater to different needs and preferences. In this guide, we will focus on how to sew your own welding cap.
The Importance of Sewing Your Own Welding Cap
Sewing your own welding cap has several advantages over buying a pre-made one. Firstly, you can customize it according to your size and style preferences. This ensures a better fit compared to store-bought ones that come in standard sizes. Secondly, you have control over the choice of material used in making the cap. This is important because choosing a flame-resistant fabric is vital for safety when welding. Lastly, sewing your own welding cap can save you money in the long run as buying fabric and making your cap is more cost-effective than purchasing pre-made ones.
Materials needed for Sewing a Welding Cap
Before you start sewing your welding cap, it’s essential to have all the necessary materials at hand. These include:
- 1 yard of flame-resistant fabric (cotton or denim are popular choices)
- Lining fabric (optional)
- Measuring tape
- Fabric marking pen/pencil
- Pins
- Sewing machine or needle/thread if hand-sewing
- Scissors
- Iron
- Sewing pattern (optional)
Choosing the Right Fabric for Your Welding Cap
As mentioned earlier, the choice of fabric for your welding cap is essential. Not all fabrics are suitable for this purpose, as they may not provide adequate protection from sparks and heat. It’s crucial to choose a flame-resistant material that can withstand high temperatures. Some popular options include cotton, denim, leather, and wool. Cotton and denim are widely used as they are easy to find and handle, while leather and wool provide more protection but can be more challenging to work with.
Creating a Sewing Pattern
Creating a sewing pattern before starting the actual sewing process can help in creating a more accurate and polished welding cap. If you’re not familiar with drafting patterns, you can find many free templates online or purchase one for a small fee. You can also use an old welding cap as a template by carefully taking it apart and tracing the pieces onto paper.
The Sewing Process
Once you have gathered all the necessary materials and have your pattern ready (if using one), it’s time to start sewing your welding cap.
- Wash and iron your fabric to remove any wrinkles or dirt.
- Place your pattern pieces on the fabric, trace them using your marking pen/pencil, and cut them out.
- If you’re lining your welding cap, repeat step 2 with the lining fabric.
- Sew all pieces together following the instructions on your pattern or using the traditional “right sides together” method.
- If you’re hand-sewing, use a backstitch or whip stitch to join the pieces.
- Once all pieces are joined, iron out any wrinkles or bumps in the fabric.
- Add any desired decorations such as embroidery or custom labels.
Final Touches: Finishing Your Welding Cap
You’re almost done! Now it’s time to add the finishing touches to your welding cap.
- Try on your cap and make any necessary adjustments to ensure a snug fit.
- Secure the seams by backstitching or running them through a serger.
- If you’re lining your welding cap, attach it to the outer fabric by stitching along the bottom edge with a ½ inch seam allowance.
- To prevent fraying, finish off the edges of your cap with a zigzag stitch or overlock stitch.
- Clean up any excess threads and give your welding cap one last ironing.
Sewing your own welding cap is not only cost-effective but also allows you to create a piece that fits your needs and style. By following the steps outlined above, you can easily create a customized welding cap that provides adequate protection while working. Remember always to use flame-resistant fabric and take safety precautions when sewing. Happy sewing!
Welcome to our comprehensive guide on how to sew welding caps. Whether you are a professional welder or just starting out, a welding cap is an essential piece of protective gear that not only offers comfort but also ensures your safety. While there are many pre-made welding caps available in the market, learning how to sew your own is not only cost-effective but also allows you to customize it according to your preferences.
In this guide, we will break down the steps required to sew a welding cap from scratch. From choosing the right fabric and materials to sewing techniques and tips, we’ve got you covered. Whether you have basic sewing skills or are an experienced seamstress, this guide will provide you with all the necessary information to create a high-quality and durable welding cap. So let’s get started!
Understanding Welding Caps
Before we dive into the sewing process, it’s essential to understand what exactly a welding cap is and its purpose. A welding cap is a headgear worn by welders to protect their head, neck, and ears from flying sparks and heat while working. It is designed with a dome-shaped crown and extended brim at the front and back to shield the neck.
Welding caps come in various styles, including soft crown, hard crown, beanie, and doo rag. Soft crown caps have no stiffening materials while hard crown ones have buckram or elastic for added structure. Beanies are fitted with a wrap-around brim that securely holds them in place during work while doo rags are designed for better coverage of the neck area.
Gathering Materials
The first step in making a welding cap is gathering all the necessary materials. The most crucial material for this project is Kevlar or flame-resistant fabric that can withstand high temperatures produced during welding processes. Other materials required include:
– Fabric scissors
– Sewing machine
– Measuring tape
– Pins
– Thread (preferably strong nylon or polyester)
– Chalk or fabric marker
– Elastic (if making a hard crown cap)
– Optional: Pattern or template for precise cuts
When choosing the fabric, look for one specifically designed for welding gear or has a high heat resistance rating. It’s also essential to ensure that the fabric is lightweight and breathable to avoid discomfort during work.
Creating a Pattern
Once you have all the materials, the next step is to create a pattern. This step is optional, especially if you are confident in cutting freehand. However, having a pattern can make the sewing process more precise and easier.
To create a pattern, measure your head using a measuring tape, starting from your forehead around your head to the back. Take this measurement and add an extra inch for seam allowance. Using this measurement, draw two straight lines on paper with six inches in between them. The first line should be equal to your head measurement plus one inch while the second one should be half of it.
Next, sketch out your desired cap shape by drawing lines from both ends of the first line to corresponding points on the second line. This will form a diamond shape that represents the top of your cap. Lastly, add half an inch along all edges for seam allowance and cut out your pattern.
Cutting and Preparing Fabric
Lay out your chosen fabric on a flat surface and place your pattern on top of it. Pin down the pattern securely onto the fabric using straight pins and use chalk or fabric marker to trace around it.
Using sharp fabric scissors, carefully cut along the traced lines, ensuring that you leave half an inch extra along each edge for seam allowance. If you are using multiple layers of fabric, make sure they are aligned before cutting.
Before sewing, it’s essential to prepare the fabric by finishing off the edges. This prevents fraying and makes your cap look more professional. To finish the edges, you can use a serger or sew a zigzag stitch along the entire edge.
Constructing the Cap
Now that your materials are ready, it’s time to start sewing your welding cap. Begin by sewing the side seams of your cap together, ensuring that you leave half an inch at both ends unsewn for seam allowance. Then, fold and press half an inch on both sides of the brim, and sew them down using a straight stitch.
Next, attach elastic to the back of your cap if you are making a hard crown. Cut a piece of elastic that is slightly smaller than the length of your cap’s back seam. Pin one end of the elastic to one end of the seam and sew it in place using a zigzag stitch. Repeat this on the other side before sewing down both sides of the elastic to secure it.
Finally, attach the brim to both sides of your cap by folding each side over and pinning it in place. Sew along these folds using a straight stitch to create a smooth edge.
Finishing Touches
To
Q: What materials do I need to sew welding caps?
A: You will need a sewing machine, fabric, thread, measuring tape, scissors, pins, and a pattern to sew welding caps.
Q: How do I choose the right fabric for welding caps?
A: It is important to choose a heavy-duty fabric that is flame-resistant such as cotton, twill, or denim. Avoid synthetic fabrics as they can melt when exposed to high heat.
Q: Can I adjust the size of the welding cap?
A: Yes, you can adjust the size of the welding cap by using a pattern or altering the measurements. Make sure to take accurate measurements for a comfortable fit.
Q: Do I need any special sewing techniques for sewing welding caps?
A: While basic sewing skills are required, there are a few techniques that are specific to sewing welding caps such as double stitching and using reinforced seams to ensure durability.
Q: Are there any safety precautions I should take while sewing welding caps?
A: Yes, it is important to wear protective gear such as gloves and safety glasses while handling the fabric and sewing near flames.
Q: Can I add additional features to my welding cap?
A: Yes, you can customize your welding cap by adding features like sweatbands, ear flaps, or reflective tape for better visibility in low-light conditions. Just make sure they are made of flame-resistant materials.
In conclusion, sewing welding caps is a valuable skill to have for anyone working in welding or fabrication industries. It not only helps protect the head and hair from sparks and debris but also adds a personal touch to one’s work attire. Through this guide on how to sew welding caps, we have discussed the essential steps and techniques required for creating a durable and comfortable cap.
Firstly, it is crucial to select the right materials, including fire-resistant fabrics like denim or cotton twill, and sturdy threads such as nylon or polyester. Proper measurements and cutting of the fabric are also important for ensuring a snug fit and a professional finish. Techniques such as using double stitches for reinforcement and adding sweatbands for comfort have been highlighted to enhance the functionality and longevity of the cap.
We have also emphasized the importance of proper safety measures while working with hot tools like irons or sewing machines. Following the recommended guidelines can prevent accidents and ensure a smooth sewing process.
Moreover, this guide has also discussed some helpful tips on customizing welding caps by incorporating embroidery or unique designs. This provides an opportunity for welders to showcase their creativity while still adhering to safety standards.
Additionally, we have emphasized the importance of practicing and being patient when learning how to sew welding caps. With time, one can improve
Author Profile
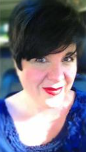
-
My name is Jill but everyone calls me Jilly. I design original cross stitch patterns inspired by vintage French and flowers. Roses are my muse.
I hope you have a cozy time stitching my patterns. Put the kettle on, relax and create a heartwarming piece of hand-embroidered art. Personalize your home and turn up the soulful charm with soulful stitchery.
My goal is to provide you with pretty patterns that promote peaceful stitching. My wish is for you to discover the gentle beauty of hand-embroidery.My patterns have been featured around the web and in Homespun Magazine and Boston Magazine. I find my bliss in cross stitch.
From 2024, I have embarked on a new venture—writing an informative blog on the “Embroidery and Cross-Stitch” niche. This blog is an extension of my passion, where I share detailed posts and respond to queries related to embroidery and cross-stitching.
The blog covers a wide range of topics from beginner tips, pattern creation, historical insights, and the therapeutic benefits of stitching. My goal is to build a community where enthusiasts can learn, share, and grow in their embroidery skills, ensuring everyone can find their own bliss in cross-stitch just as I did.
Thank you to all my customers and readers who have supported Sew French. Your kind emails, photos of completed patterns, and continual encouragement fuel my dedication to this beautiful craft. Join me in stitching a world of beauty and peace, one pattern at a time.
Latest entries
- May 24, 2024Machine Using Tips And MaintenanceUnleashing the Mystery: Demystifying the Purpose of Feed Dogs on a Sewing Machine
- May 24, 2024SewingUnlocking the Magic: Exploring the World of Computerized Sewing Machines
- May 24, 2024SewingUnleashing Creativity: Mastering the Art of Sewing with Fat Quarters
- May 24, 2024SewingTo Wash or Not to Wash: The Great Debate on Pre-Washing Fabric Before Sewing