Unraveling the Mystery: The Power of Serging Sewing
Have you ever looked at a beautifully finished seam and wondered, “How did they do that?” The answer is serging sewing. This technique creates neat and professional-looking edges on fabric, making it a top choice among avid sewers and seamstresses. Whether you’re new to the world of sewing or a seasoned pro looking to expand your skills, understanding what serging sewing is and how it works can take your projects to the next level. In this article, we’ll delve into the basics of serging sewing and explore its many benefits. Let’s get ready to elevate your crafting game!
Serging sewing is a popular technique used in the garment and textile industry to create clean, finished edges on fabric. It involves using a specialized sewing machine called a serger or overlock machine to trim, encase and stitch fabric together in one step. This process results in a professional and neat finish that prevents fraying and adds durability to the final product.
History of Serging Sewing
The history of serging sewing can be traced back to the early 19th century when French inventor, Joseph Merrow, patented the first overlock sewing machine. However, it was not until the mid-20th century that serging became a widely used technique in the textile industry. Serge manufacturing quickly became popular due to its efficiency and cost-effectiveness. Today, serging is an essential part of the production process for many clothing manufacturers worldwide.
How Serging Sewing Works
Serging sewing involves using three to five threads to create a finished edge on fabric. The machine trims excess fabric while simultaneously encasing the edge with thread, creating a secure seam. The needles used in serging machines form multiple rows of stitches that interlock with each other to prevent unraveling. The fifth thread is often used as an optional cover stitch for added strength and a polished finish.
Differences Between Serging Sewing and Traditional Sewing
The most significant difference between traditional sewing and serging sewing is in the type of stitches created by each method. Traditional sewing typically uses only one thread to sew two pieces of fabric together, resulting in a visible seam with raw edges that require additional finishing techniques such as folding or hemming. On the other hand, serging creates a professional-looking seam with trimmed edges that do not require further finishing.
Another difference between these two techniques is speed and efficiency. Serging sewing is much faster than traditional sewing, as it combines several steps into one, reducing the production time significantly. Additionally, serging machines can work with a wider range of fabric types and thicknesses compared to traditional sewing machines.
Benefits of Serging Sewing
Serging sewing offers several benefits that make it a preferred technique in the textile industry. Firstly, serging creates a strong and durable seam that prevents unraveling and fraying of fabric edges. This means that garments made using this technique will last longer, making them more cost-effective for both manufacturers and consumers.
Secondly, serging is a fast and efficient process that enables manufacturers to produce garments in bulk without compromising on quality. This makes it an essential process for large-scale clothing production.
Finally, serged seams have a professional and clean finish, which adds value to the final product. This is especially important in the competitive textile industry, where high-quality finishes are highly valued.
Limitations of Serging Sewing
While serging sewing has many benefits, it also has some limitations that may not make it suitable for all projects. One primary limitation is the need for specialized equipment. Serging machines are not as common or widely available as traditional sewing machines, making them more expensive to purchase and maintain.
Moreover, serged seams may not be ideal for all types of garments or fabrics. For instance, delicate fabrics such as silk or chiffon may easily get damaged when trimmed by a serger machine. In such cases, traditional sewing methods may be more suitable.
Applications of Serging Sewing
Serging sewing has numerous applications in the garment and textile industry. It is commonly used in garment manufacturing to create professional finishes on clothing items such as t-shirts, dresses, skirts, and pants. Serged seams are also popular in sportswear or activewear due to their durability and flexibility.
In addition to clothing, serging sewing is also useful in home decor projects such as curtains, pillows, and tablecloths. The clean finish created by serging adds a touch of professionalism to these items, making them an excellent choice for home decoration.
In conclusion, serging sewing is a versatile and efficient technique used in the textile industry to create professional finishes on fabric edges. It has been around for centuries and has evolved to become an essential part of garment production. Although it has its limitations, the benefits of serging make it a valuable technique for manufacturers looking to produce high-quality and long-lasting products. So next time you see a neatly finished edge on your favorite piece of clothing or home decor item, remember that it was most likely achieved through the process of serging sewing.
Overview of Serging Sewing
Serging sewing, also known as overlock stitching, is a specialized technique used in sewing to finish the edges of fabric. This type of stitch creates a clean and professional-looking edge that prevents the fabric from fraying. It is commonly used on garments, home decor items, and other sewn projects.
History of Serging Sewing
The serger machine was first introduced in the early 19th century by the Merrow Machine Company. However, it wasn’t until the late 20th century that serging sewing became popular among home sewers due to the affordability and accessibility of serger machines. Initially, serging was primarily used in the garment and textile industry for its speed and efficiency in producing finished edges.
How Does Serging Sewing Work?
Serging sewing uses multiple threads to create a strong and durable seam which helps prevent fabric from unraveling. The machine makes loops around the edges of the fabric while trimming off any excess material. It can also simultaneously bind or hem fabrics while serging. Sergers are typically equipped with multiple needles and cutting blades, allowing for quick and precise stitching.
Benefits of Serging Sewing
One of the biggest benefits of using serging sewing is its ability to prevent fraying on fabric edges. This type of stitch is ideal for finishing woven fabrics such as cotton, linen, denim, and wool. Serge seams are also stretchy, making them perfect for knit fabrics that require flexibility without breaking stitches.
Another advantage of using a serger machine is its speed compared to traditional sewing machines. With multiple threads being used at once and no need for frequent bobbin changes, sergers allow for faster production times on projects.
Additionally, sergers have various settings and attachments that allow for different types of stitches such as rolled hems, lettuce edges, and flatlocking. These versatile stitching options make serging sewing a popular choice among sewers looking to add unique and professional finishes to their projects.
When to Use Serging Sewing
Serging sewing is commonly used for finishing edges on garments such as skirts, dresses, and shirts. It is also widely used in the production of home decor items like curtains, pillowcases, and tablecloths. If you are working with delicate or lightweight fabric that tends to fray easily, serging can help prevent any unwanted fraying during the construction process.
Another scenario where serging sewing is useful is when you want to create a professional-looking finish without the bulk of traditional seam allowances. This makes it an excellent choice for active wear and lingerie that requires comfortable and stretchy seams.
Challenges of Serging Sewing
While serging sewing offers many benefits, it also comes with its own set of challenges. Getting the tension right can be tricky since multiple threads are used at once. It may take some trial and error to find the ideal tension settings for different types of fabric.
Another challenge when using a serger is blade positioning. If not properly adjusted, the cutting blade may cut off more fabric than intended or leave behind unwanted frays on the edge of the fabric.
Additionally, sergers tend to be louder than traditional sewing machines due to their faster speed and multiple threads being used simultaneously. This can make it challenging to use in quiet environments such as late-night sewing sessions.
Serging sewing is a specialized technique that provides a professional finish on various types of fabrics. Its versatility makes it a popular choice among sewers for creating durable seams, decorative finishes, and preventing fraying. While there may be challenges when first using a serger machine, practice and proper adjustments can result in perfectly finished projects. Now that you understand the basics of serging sewing, you can confidently add this technique to your sewing repertoire.
Q: What is serging sewing?
A: Serging sewing, also known as overlock sewing, is a method of creating a seam that binds fabric edges while also trimming off excess fabric.
Q: What types of machines are used for serging sewing?
A: Serging sewing requires the use of a serger machine, which is specifically designed for this type of stitch. Regular sewing machines cannot produce the same results.
Q: What are the benefits of using a serger machine for serging sewing?
A: Using a serger machine allows for faster and more efficient binding and trimming of fabric edges, resulting in a professional-looking finish. It also prevents fraying and creates strong, durable seams.
Q: Can I use a serger machine for all my sewing projects?
A: A serger machine is best suited for finishing edges and creating seams. It may not be suitable for intricate or decorative stitching, so it may not be suitable for all types of sewing projects.
Q: Are there different types of stitches that can be created with a serger machine?
A: Yes, there are several types of stitches that can be created with a serger machine depending on the project and desired effect. Some common ones include 4-thread overlock stitch, rolled hem stitch, and flatlock stitch.
Q: Is it necessary to have experience to use a serger machine for serging sewing?
A: While having some experience with regular sewing can make it easier to learn how to use a serger machine, it is not necessary. Many beginners have successfully learned how to use it through online tutorials or classes.
In conclusion, serging sewing is a technique that produces a neat and professional finish to fabric edges, preventing fraying and enhancing the overall appearance of a garment. This technique involves using a serger or overlocker machine, which trims the raw edges of fabric while simultaneously sewing them together with an overlock stitch. Serging sewing has a wide range of applications, from creating finished edges on clothing items such as t-shirts and underwear to hemming curtains and decorative items. It also offers several advantages over traditional sewing techniques, such as speed, efficiency, and durability.
By understanding the basics of serging sewing and mastering its various settings, one can achieve high-quality results in their projects. It is essential to select the right type and weight of thread, adjust tension and stitch length settings properly, and practice on scraps of fabric before beginning a project. Additionally, investing in a good quality serger machine can make the process simpler and more efficient.
However, like any technique or skill, mastering serging sewing takes time and practice. It is important to be patient and not get discouraged by initial hiccups. By consistently honing one’s skills with proper techniques and tips, anyone can achieve beautifully finished seams using this versatile method.
Moreover, serging sewing is not only limited to
Author Profile
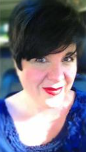
-
My name is Jill but everyone calls me Jilly. I design original cross stitch patterns inspired by vintage French and flowers. Roses are my muse.
I hope you have a cozy time stitching my patterns. Put the kettle on, relax and create a heartwarming piece of hand-embroidered art. Personalize your home and turn up the soulful charm with soulful stitchery.
My goal is to provide you with pretty patterns that promote peaceful stitching. My wish is for you to discover the gentle beauty of hand-embroidery.My patterns have been featured around the web and in Homespun Magazine and Boston Magazine. I find my bliss in cross stitch.
From 2024, I have embarked on a new venture—writing an informative blog on the “Embroidery and Cross-Stitch” niche. This blog is an extension of my passion, where I share detailed posts and respond to queries related to embroidery and cross-stitching.
The blog covers a wide range of topics from beginner tips, pattern creation, historical insights, and the therapeutic benefits of stitching. My goal is to build a community where enthusiasts can learn, share, and grow in their embroidery skills, ensuring everyone can find their own bliss in cross-stitch just as I did.
Thank you to all my customers and readers who have supported Sew French. Your kind emails, photos of completed patterns, and continual encouragement fuel my dedication to this beautiful craft. Join me in stitching a world of beauty and peace, one pattern at a time.
Latest entries
- May 24, 2024Machine Using Tips And MaintenanceUnleashing the Mystery: Demystifying the Purpose of Feed Dogs on a Sewing Machine
- May 24, 2024SewingUnlocking the Magic: Exploring the World of Computerized Sewing Machines
- May 24, 2024SewingUnleashing Creativity: Mastering the Art of Sewing with Fat Quarters
- May 24, 2024SewingTo Wash or Not to Wash: The Great Debate on Pre-Washing Fabric Before Sewing